OUR GOAL
DH09 Aims to be the first student team that will realize a scaled-up hyperloop system and showcase its operation at the European Hyperloop Center.
.jpeg)
SCALE UP
At Delft Hyperloop, we build a scaled model pod each year to test the core principles of Hyperloop technology. This allows us to explore innovative solutions, push technological boundaries, and contribute to the global development of sustainable, high-speed transportation.
This year, we're taking a big step forward by building a pod 2 to 3 times larger, as we scale up. This enables us to compete at the European Hyperloop Week and test on the EHC track.
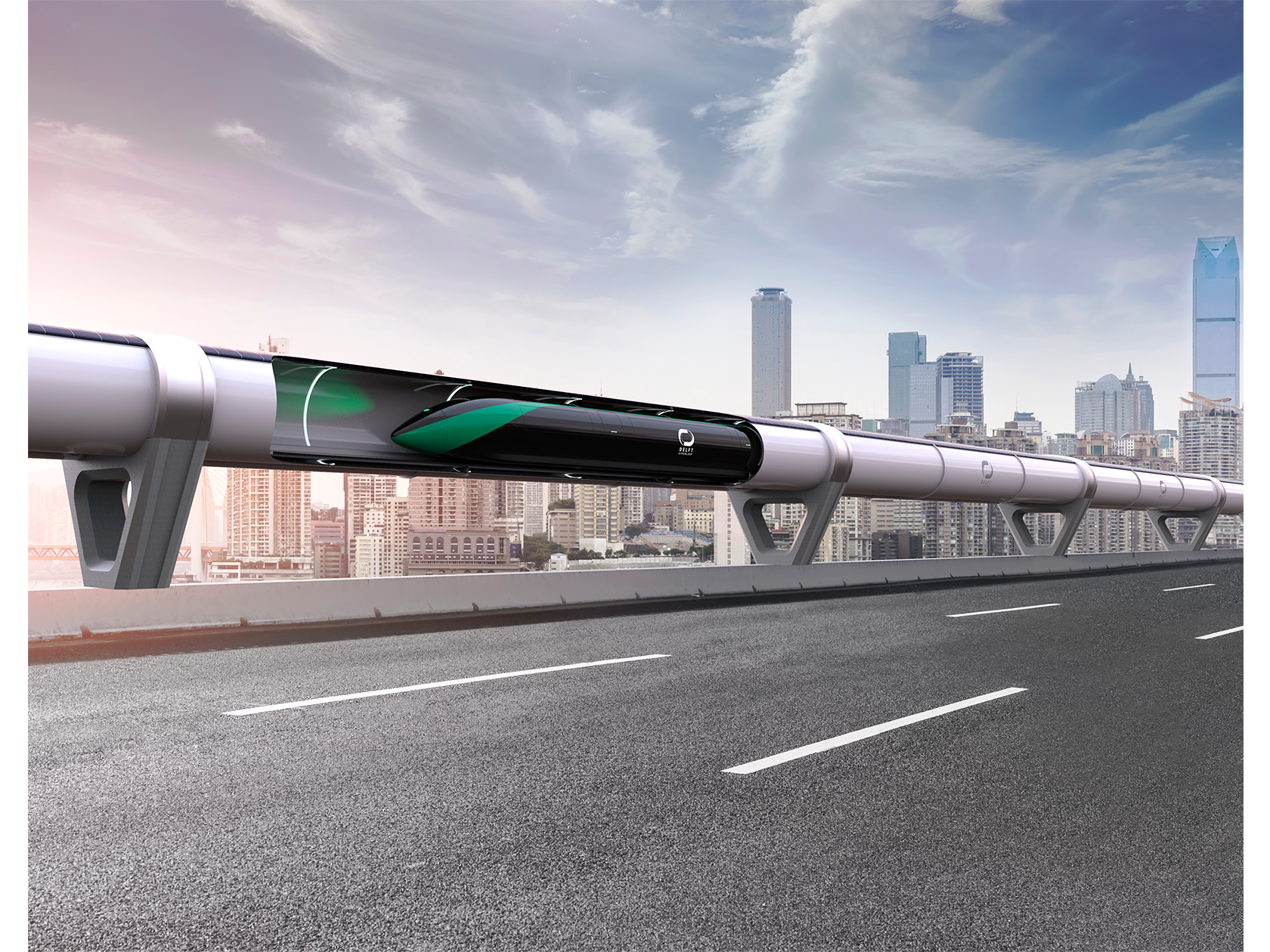
INFRASTRUCTURE
One of the greatest challenges in bringing the Hyperloop to reality is creating the necessary infrastructure. With tracks crossing multiple countries, aligning international standards is crucial, alongside addressing safety and regulatory challenges. This year, by testing our pod on the EHC track, we contribute to developing a standardized infrastructure, a key step toward making the Hyperloop a global reality.
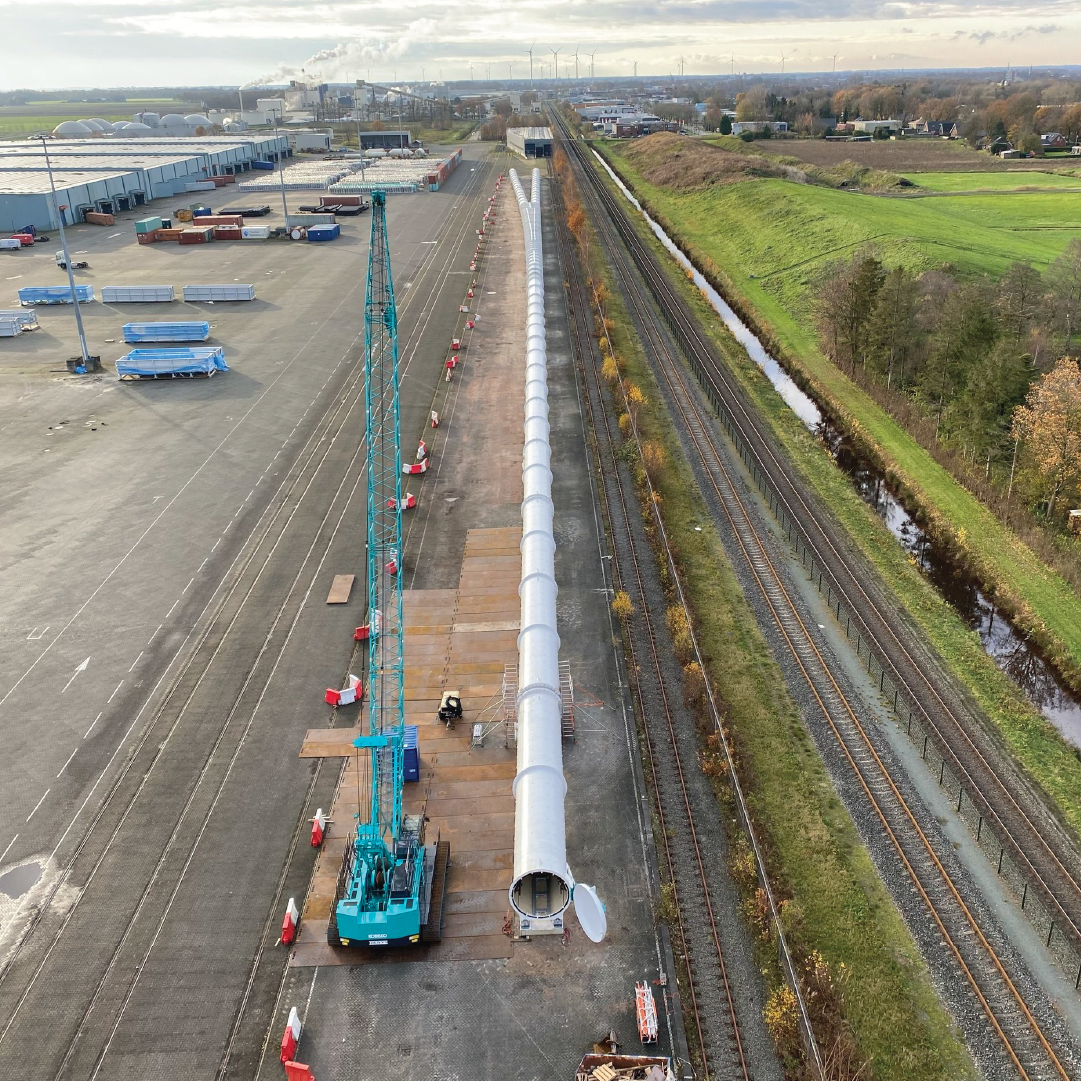
EHC
The European Hyperloop Center (EHC) is a non-profit organization based in Veendam, Netherlands, dedicated to accelerating Hyperloop development. With its state-of-the-art track in Groningen, the EHC positions the Netherlands as a global epicenter for Hyperloop innovation. This year, Delft Hyperloop is excited to participate in the European Hyperloop Week, testing our pod on the EHC track and contributing to the advancement of Hyperloop technology and infrastructure.